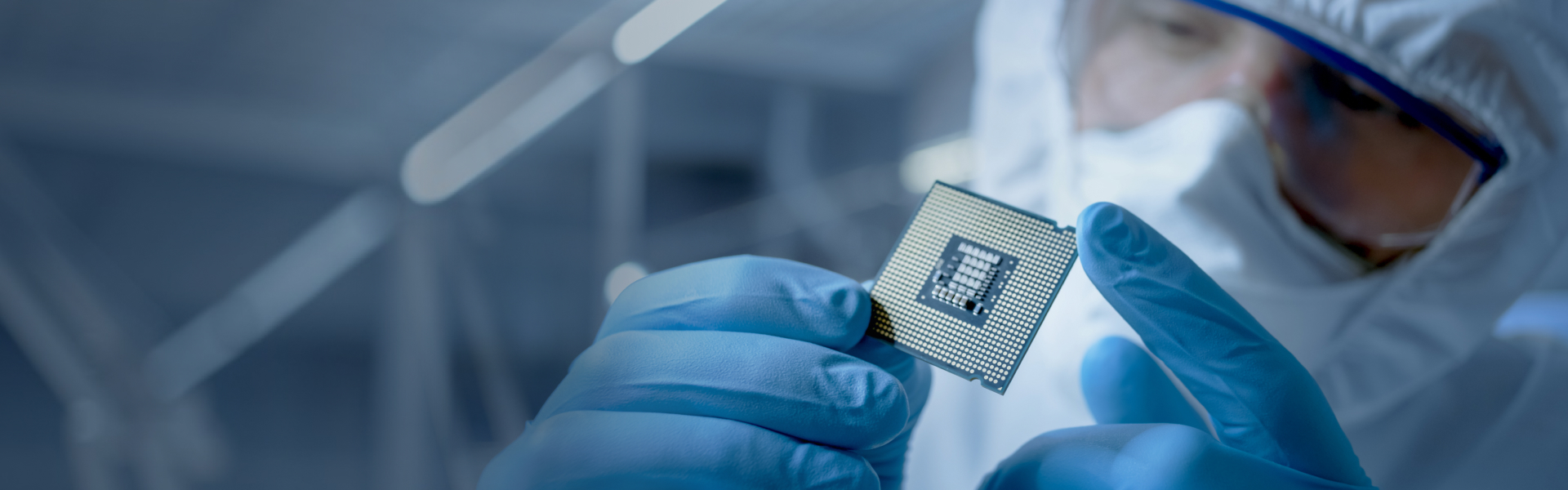
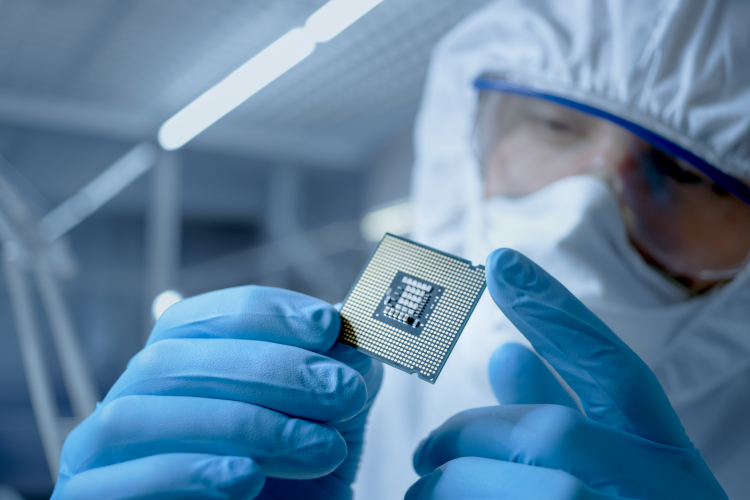
Quality
To be the benchmark and leading domestic enterprise of automotive electronics in China with innovative technolody and high-qulity products.
Quality Policy & Objectives
We are committed to providing products with high reliability, innovative solutions and good services to meet the expectations of our customers. Quality is the base. With our?quality?management?system,?we?have established a quality culture that incorporates quality design, no compromises on manufacturing quality and continuous improvements.
-
Quality KPI
Set KPI yearly and improve continuously
Quality Objectives -
Quality First
"Quality First" is our first priority during product life cycle
Quality Mission -
Zero Defects
Zero defect is our quality goal
Quality Vision
Quality Management System
-
ISO9001
TüV Rheinland
-
ISO26262
TüV Rheinland
New Product Design & Development Process APQP
-
Project request
Marketing requests
Engineers submit new ideas
Project background
Cost Analysis & ROI
Marketing & Sales Strategy
Project Goals and Targets
Schedule and Team Resource
Project Risks and Mitigation
P0 -
Product definition and project planning
Marketing requests
Engineers submit new ideas
Product Prelim BOM
Prelim Special product characteristics
Product requirements
Detailed Project Plan
P1 -
Product design and process development
Product requirements
Technical risk assessment/initial DFMEA
Tape out checklist
Datasheet draft version
Engineering drawing (POD,,bonding diagram)
BOM and Special product characteristics
Subcon Selection and verification
Reliability strategy defined
Test development
Product validation
Lessons Learnt
P2 -
Product and process verification
Product requirements
Verification plan
Product application verification Result
Robustness test Result (High current HTOL)
Subcon process verification result
Product automatic test release result
Document official released to DCC
ERP system ready
Lessons Learnt
P3
-
Safe launch and pre-series production
?Product and process verification result
Safe Launch data analysis and improvement
Subcon management result
Customer PPAP preparation
Project Lessons Learnt
P4 -
Project closed and mass production
Customer order and forecast
Project closed and Lessons Learnt Summary
Project performance evaluation
Subcon performance monitor
P5
質(zhì)量為基 創(chuàng)新為本
-
PPAP
Strictly adhere to the Production Part Approval Process of the automotive industry.
-
Supplier Management
Self-developed Production Quality Control System (PQCS), real-time monitoring of production status, and effective early warning of production anomalies.
-
APQP
Strictly adhere to the automotive electronics research and development process, focusing on the forward development of chip technology.
-
Reliability/Robustness
Lab ATE BenchHave chip reliability testing strictly adhere to AEC-Q100 standard, have double and bottom testing for some key items to verify chip robustness. Have chip testing and validation by standardized lab.
Engage in research and development, production, and operations strictly in accordance with automotive industry quality system.
IATF16949
ISO9001/26262
Customer Demands
Quick response, pre-sales, and after-sales support.
Continuous improvement
-
Reliability Qualification
LEN selected a mature automotive electronic fab process, validated by wafer reliability and robustness testing.
LEN's selected a mature automotive electronic packages process from packaging factory.
Automotive product reliability testing follows AEC Q100 Grade 1 (-40°C~125°C);
Testing methods referencing the corresponding JEDC standards.
-
Robustness Testing
Conducting experiments under conditions exceeding product requirements to identify product weaknesses and design margins. Improving quality through enhancements in both product and process design.
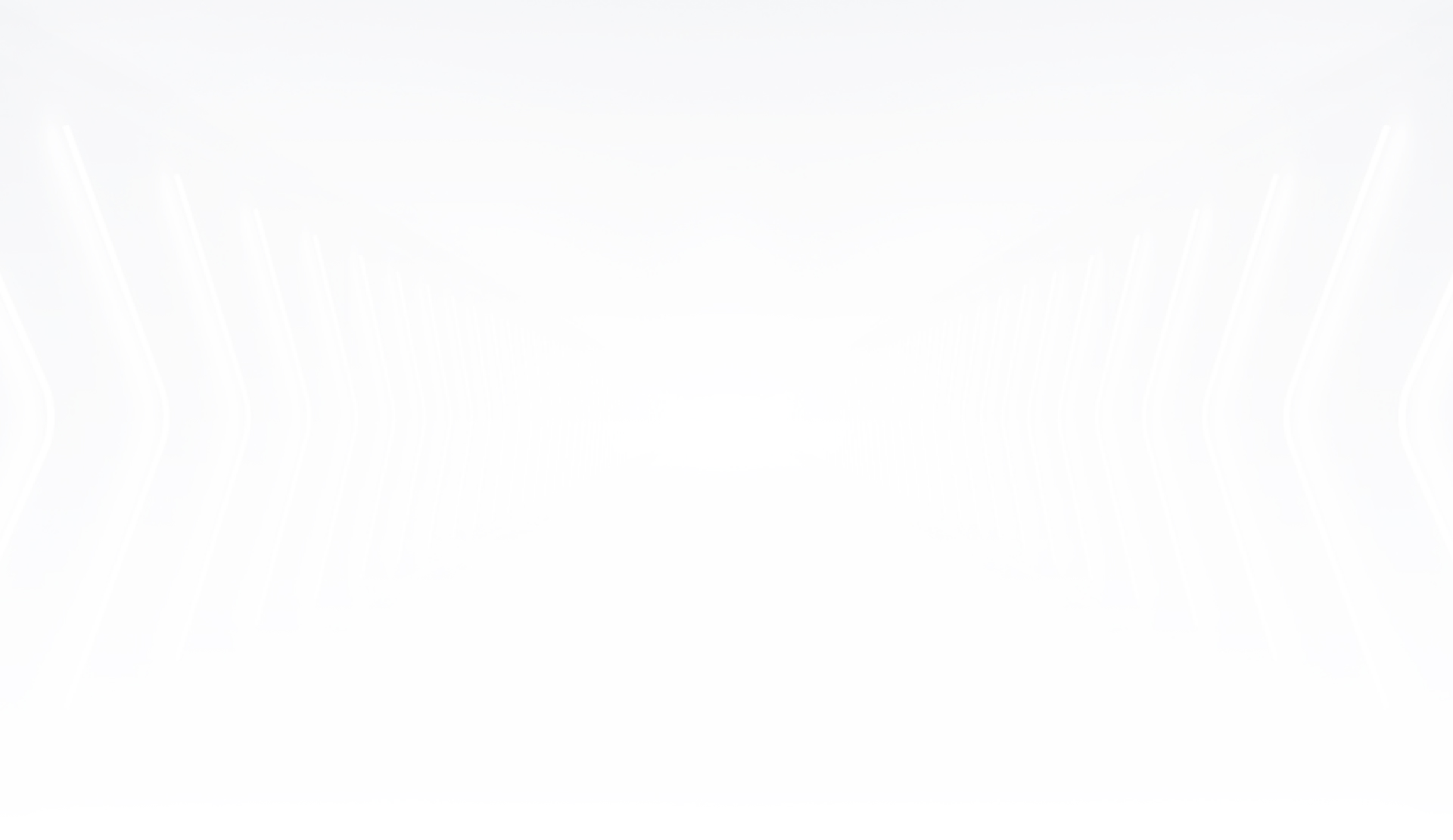
Customer Quality Service
7 / 7